Proper Gage Selection
THE GAGE FOR YOUR JOB
Since the cost of gaging is a definite cost of manufacture, certain practicalities must be recognized in regard to maximum metal limit and minimum metal limit gages. In the first place, absolute accuracy cannot be obtained commercially since the gage maker must have some tolerance. The smaller the tolerance, the more expensive the gage to manufacture.
In the second place, absolute size is impossible to maintain since gages wear with use. Recognition of these facts leads to the necessity of making a proper selection of gages if gaging costs are to be kept to a minimum. The selection of the proper gage will be determined by consideration of the number of parts to be gaged; the materials from which these parts are made; the tolerance, design and material of the gages.
TOLERANCE AS A FACTOR IN GAGE SELECTION
Theoretically the actual size of the gage should be the absolute maximum and absolute minimum size of the part tolerance. This would produce maximum acceptance of usable parts but the exclusive use of basic gages would be very expensive because of their short wear life.
It is more practical to check the part as it is machined with working gages of “Y” tolerance or high limit “X” tolerance. Inspection gages of either low limit “X” tolerance or “w” tolerance are used to check the acceptance or non-acceptance of the part. In a “Y” tolerance gage, the actual size of the gage is moved toward the middle of the product limit.
This, together with the gage manufacturer’s tolerance, gives about fifteen percent of the part tolerance as gage wear life. In normal operation some parts would be in this low fifteen percent and therefore rejected by a “Y” tolerance or high limit “X” tolerance gage, even though the parts were within the product tolerance limit.
Absolute limit, or “W” tolerance gages, which have very little wear life since they are on basic size, can be used to re-inspect the parts rejected by these gages.
By this combined use of gages of various tolerances, it is possible to obtain maximum gage wear life and hence low unit gaging costs; while at the same time having the maximum acceptance of usable parts.
No Go gages are not made in “Y” tolerance although in some situations a special plus tolerance No Go gage is used. Since this gage is outside the product part tolerance, marginal parts must be re-inspected with a high limit “X” or “W” tolerance gage in order to eliminate oversize parts.
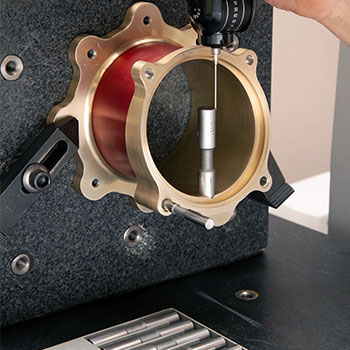
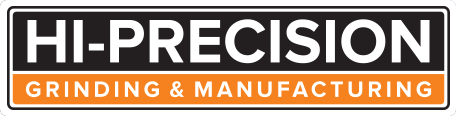